Ho dato un’occhiata alla più grande fabbrica offshore di Intel | ENBLE
Ho guardato ENBLE, la più grande fabbrica offshore di Intel.

È raro vedere un gigante della tecnologia aprire le porte per mostrare come opera realmente. Ma è esattamente ciò che Intel aveva in mente quando ha invitato la stampa globale e i rappresentanti dei media a visitare le sue fabbriche in Malaysia. Come parte del suo evento Tech Tour 2023, il produttore di chip ci ha dato una visione dettagliata di come viene realizzato un processore. Ho imparato molto, ma prima di condividere la mia esperienza, ecco una breve panoramica sulla storia dell’azienda e i piani futuri in Malaysia.
Intel ha stabilito la sua prima sede offshore in Malaysia nel 1972 con un totale di 100 dipendenti. Oggi, ci sono due importanti strutture a Penang e Kulim che si estendono per quasi 900.000 mq con 15.000 dipendenti.

Con la crescente domanda e per stare al passo con la sua strategia IDM 2.0, Intel sta già ampliando la copertura delle sue strutture. Una nuova struttura avanzata di confezionamento chiamata Pelican e una struttura di assemblaggio e test chiamata Falcon sono attualmente in costruzione e si prevede che saranno operative nei prossimi due anni. L’azienda ha anche previsto un’area totale di 7 milioni di piedi quadrati, con oltre 2 milioni di piedi quadrati di spazio di produzione, espansi su 16 edifici in futuro.
Visita a Intel Malaysia
Il tour è stato diviso in due giorni, inizialmente abbiamo visitato l’impianto di assemblaggio e test di Penang (PGAT). È qui che i dies in silicio vengono assemblati, convalidati e testati per gli errori. Ma è nell’impianto di Kulim che la magia inizia. L’impianto Intel Kulim Die Sort Die Prep o KMDSDP è un impianto all’avanguardia per il trattamento delle wafer di silicio, la materia prima che costituisce i migliori processori.
Questa fabbrica riceve le wafer di silicio dagli impianti di fabbricazione, effettua processi di preparazione dei dies e successivamente li categorizza per l’assemblaggio del pacchetto e i test presso vari impianti di assemblaggio/test Intel in tutto il mondo. L’impianto KMDSDP si trova sulla terraferma, a differenza dell’impianto di Penang che si trova sull’isola stessa, il che significava un viaggio in autobus più lungo attraverso un ponte che si affaccia sul mare.
- Cos’è Thunderbolt 5? | ENBLE
- La generazione di intelligenza artificiale per Photoshop è arrivata...
- Questo pericoloso nuovo malware per Mac ruba le informazioni della ...

Una volta arrivati a Kulim, ci è stata fornita una breve presentazione e ci è stato chiesto di indossare tute speciali con protezioni per la testa e la barba prima di poter entrare. Questo era necessario poiché le aree di produzione devono rimanere prive di polvere. Naturalmente, questo significava anche che non ci era consentito portare nulla all’interno, inclusi telefoni, fotocamere o altri dispositivi di registrazione.
Preparazione dei dies, classificazione dei dies

L’impianto KMDSDP è responsabile di due operazioni principali: la preparazione dei dies e la classificazione dei dies. Nella fase di preparazione dei dies, vengono ricevute wafer complete da 300 mm dagli impianti di fabbricazione e vengono attaccate a un foglio flessibile di mylar. Questi sono fogli semitrasparenti e sono necessari per assicurare che ogni die rimanga nella posizione corretta dopo essere stato tagliato e separato.
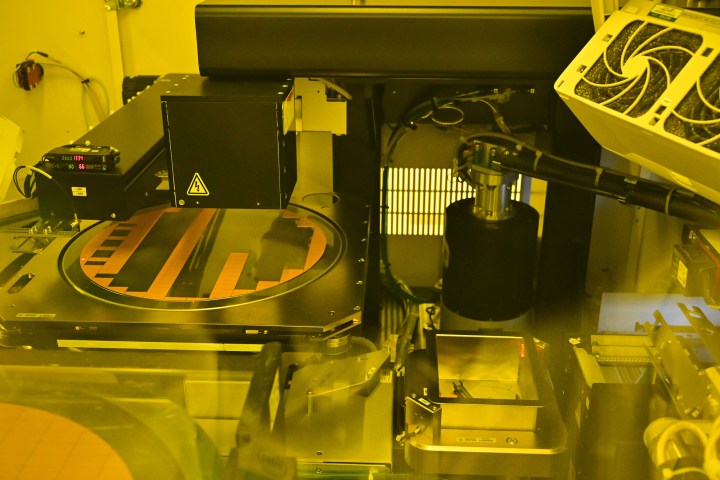
A seconda del tipo di processore, questi fogli di wafer vengono sottoposti a processi multipli, tra cui rettifica, incisione laser e taglio meccanico per creare chip individuali. Successivamente, utilizzando una combinazione speciale di vuoto e luce UV, i chip vengono separati dal mylar. Questi chip individuali vengono quindi collocati in vassoi utilizzando bracci robotici e vengono inseriti in scatole di plastica più grandi prima di essere trasportati all’operazione di classificazione successiva.
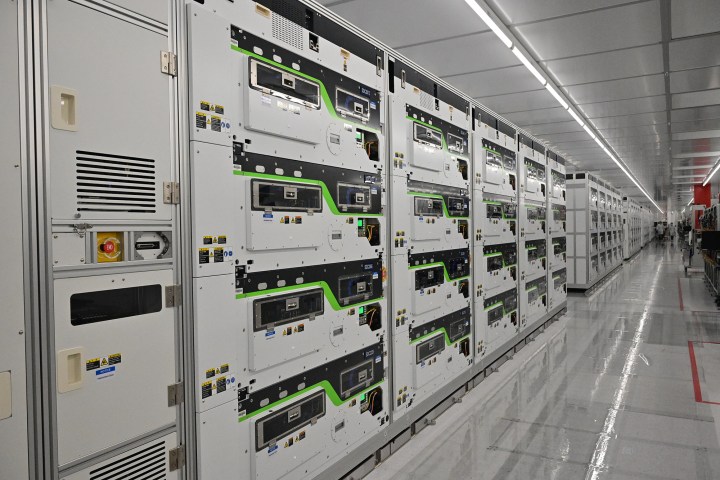
Successivamente, ciascuno di questi chip viene sottoposto a test per individuare eventuali difetti e contemporaneamente viene ordinato. Per fare ciò, Intel utilizza moduli di ordinamento massicci che sono grandi quanto un autobus e hanno un totale di 20 celle di test individuali. Ogni cella di test pesa circa 1000 libbre e per manovrarle c’è un meccanismo di sollevamento appositamente progettato che fluttua sopra il pavimento utilizzando un cuscinetto d’aria proprio come un hovercraft. Sembra quasi magico muovere questo enorme pezzo di trasporto con una sola mano.
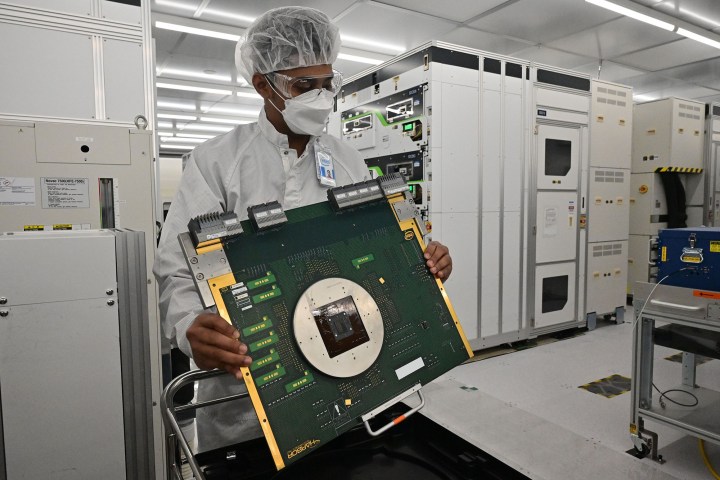
I vassoi vengono caricati da un’estremità e vengono poi distribuiti tra le varie celle di test. Poiché ogni cella di test funziona in modo indipendente, gli operatori possono accedere a una cella di test da un modulo di ordinamento per scopi di manutenzione. Ogni chip viene testato utilizzando una scheda di prova dotata di migliaia di aghi sottili, più sottili di un capello umano, che si collega al circuito integrato all’interno dell’attrezzatura di test. Questa scheda di prova misura le caratteristiche elettriche dei circuiti del chip per valutare l’affidabilità e individuare eventuali difetti. Tutti i test vengono effettuati automaticamente mentre un operatore monitora l’intero processo utilizzando vari monitor.

C’erano anche alcuni speciali veicoli di guida automatica (AGV) che hanno attirato l’attenzione di tutti principalmente a causa del loro tono simile a un camion dei gelati. Il loro compito principale è gestire il movimento dei lotti tra gli spazi di stoccaggio e l’attrezzatura di test. Richiedono quasi zero intervento umano e si muovono intorno all’installazione lungo percorsi dedicati.
Una volta che un vassoio ha completato la fase di test e caratterizzazione, viene restituito all’area in cui la wafer è stata tagliata in chip singoli. I chip che non superano la fase di test vengono raccolti separatamente e vengono scartati o riciclati. I vassoi con chip che hanno superato con successo tutti i test vengono ordinati e assegnati a un certo SKU (Core i9, Core i7, ecc.). Ogni chip viene estratto dal vassoio e sigillato tra due strati di pellicola che vengono poi avvolte su un rullo, in modo da poter essere trasportate alle strutture di assemblaggio e test situate in tutto il mondo, per ulteriori lavorazioni.

Passiamo all’assemblaggio e al test
La parte successiva del tour includeva una visita all’impianto di assemblaggio e test di Penang (PGAT), che si trova sull’isola di Penang. Questo impianto di produzione si concentra sull’assemblaggio e il test di vari chip in milioni ogni giorno. In sostanza, tutti i rulli vengono ricevuti in questo impianto e poi ogni chip viene rimosso, confezionato e testato prima di essere pronto per arrivare nei negozi.

Il processo di assemblaggio e test presso PGAT ha sei fasi chiave. Tutto inizia con il processo di Chip Attach in cui il die o il chip viene attaccato al substrato, il materiale di base della CPU. Questo viene fatto utilizzando il processo di bonding chip-su-chip Foveros face-to-face (F2F) che è stato introdotto per la prima volta nel 2019. Il processo richiede un’elevata precisione poiché ogni imperfezione può causare gravi danni al chip. Viene applicato uno strato aggiuntivo di sottofondo epossidico in modo uniforme per eliminare eventuali fessure microscopiche tra il die e il substrato.
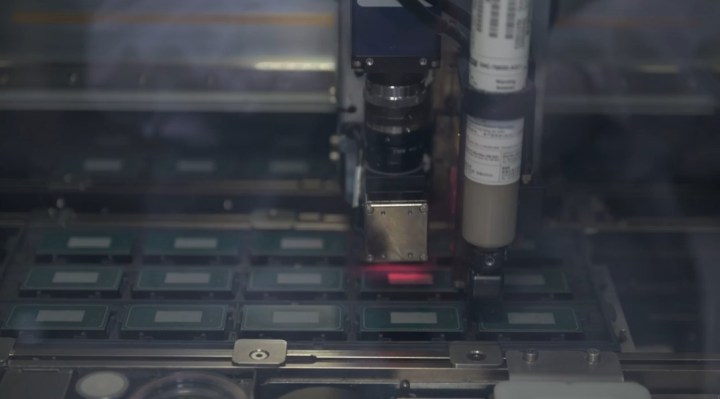
Il passo successivo è attaccare l’Integrated Heat Spreader (IHS) o il coperchio della CPU. Questo aiuta nella dissipazione efficiente del calore nei sistemi degli utenti finali. Viene utilizzata una macchina per applicare prima una certa quantità di materiale di interfaccia termica sul die, seguito dall’adesivo in modo che il coperchio IHS possa essere posizionato. Ora abbiamo un prodotto finito pronto per l’azione. Ma prima di ciò, deve passare attraverso alcuni rigorosi test.
Una volta che la CPU è pronta, deve sottoporsi a vari test per garantire che il prodotto funzioni come previsto. Questo avviene presso il Laboratorio di Progettazione e Sviluppo a PG16 a Penang.
Prima di tutto c’è il test di burn-in durante il quale Intel espone i chip a temperature e tensioni elevate per identificare ed eliminare eventuali difetti. I chip che superano con successo questo test passano poi al test elettrico, che include la verifica di tutte le tracce elettriche e la funzionalità. Infine, i chip devono sottoporsi alla fase di test PPV che serve a convalidare la selezione del prodotto della piattaforma per confermare la funzionalità nei sistemi informatici dei clienti effettivi che eseguono Windows, Linux o altri ambienti operativi. Essenzialmente è un processo che simula un ambiente cliente e testa anche vari aspetti come la memoria, le linee PCIe, ecc.
L’ultima fase del tour includeva una visita al System Integration and Manufacturing Services (SIMS), una fabbrica speciale che produce attrezzature per testare e convalidare le CPU durante la loro produzione. Questa struttura non solo produce attrezzature di test per Intel Malaysia, ma le spedisce anche in varie altre strutture Intel in tutto il mondo.

Abbiamo avuto l’opportunità di vedere alcune delle attrezzature di test, tra cui il tester High Density Burn-In (HDBI), il tester High Density Modular Tester (HDMT) e il tester System Level Tester (SLT). Il tester HDBI viene utilizzato per eseguire test di stress di burn-in ad alta temperatura e tensione su CPU Intel, mentre l’HDMT offre la possibilità di eseguire test di classe o di backend. Intel afferma che questo tester viene utilizzato nelle loro fabbriche e laboratori per lo sviluppo di nuovi prodotti e la produzione di CPU. Infine, lo SLT viene utilizzato per confermare che i prodotti Intel funzioneranno in un ambiente simile a quello del cliente. Ogni tester è progettato per allinearsi alle caratteristiche e ai requisiti precisi della CPU, garantendo una copertura di test sufficiente e mantenendo la qualità del prodotto.
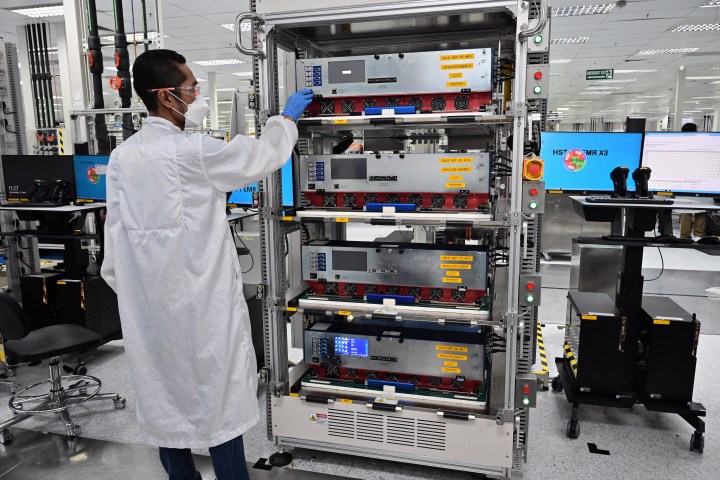
Un’esperienza senza precedenti
L’intera esperienza di assistere e comprendere il processo di produzione delle CPU è veramente senza precedenti. Sono rimasto assolutamente impressionato dall’immensa scala delle operazioni e dalle complessità coinvolte nella produzione di una singola unità del prodotto finale. L’intero stabilimento di produzione funziona come una macchina ben oliata, ma è sostenuto da varie complessità e dalla dedizione instancabile della forza lavoro dell’azienda.
Esplorare le diverse sezioni degli stabilimenti di produzione non solo mi ha fornito una comprensione più approfondita di come l’azienda realizza i suoi chip di alta qualità, ma mi ha anche offerto un chiaro sguardo sul futuro di Intel. Il suo impegno nel presentare cinque nodi entro i prossimi quattro anni potrebbe sembrare una strategia di marketing, ma sembra del tutto fattibile, soprattutto data l’impressionante capacità delle sue fabbriche di produzione. Queste fabbriche garantiscono anche che l’azienda sia in linea con la sua strategia IDM 2.0 per la produzione, l’innovazione e la leadership dei prodotti.
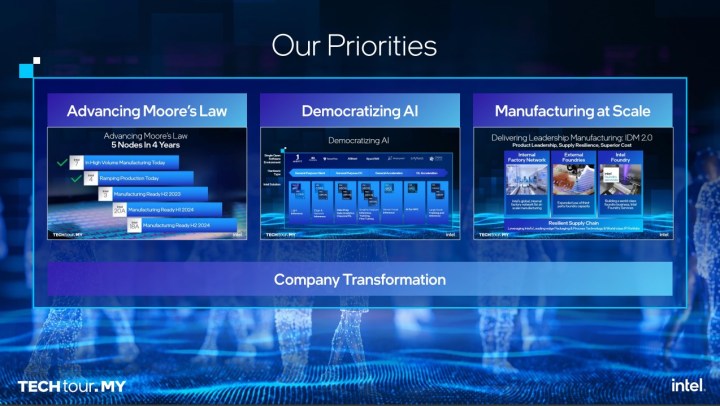
Tuttavia, è importante riconoscere che Intel non avrà un percorso senza ostacoli verso il successo. C’è una forte concorrenza da parte di rivali come AMD e altri produttori di chip, e solo il tempo dirà se Team Blue riuscirà a mantenere il suo primato nel settore.
Per ora, ci aspettiamo che Intel lanci nuovi chipset mobili entro la fine dell’anno con il nome in codice ‘Meteor Lake’ della 14a generazione. Si prevede che sarà una pietra miliare importante per l’azienda in quanto utilizzerà il processo Intel 4, diventando la prima linea di chip a utilizzare il processo a 7 nm. Poco dopo, ci sono voci che i processori desktop di nuova generazione arriveranno anche come un aggiornamento alla linea di chip Raptor Lake della 13a generazione esistente.